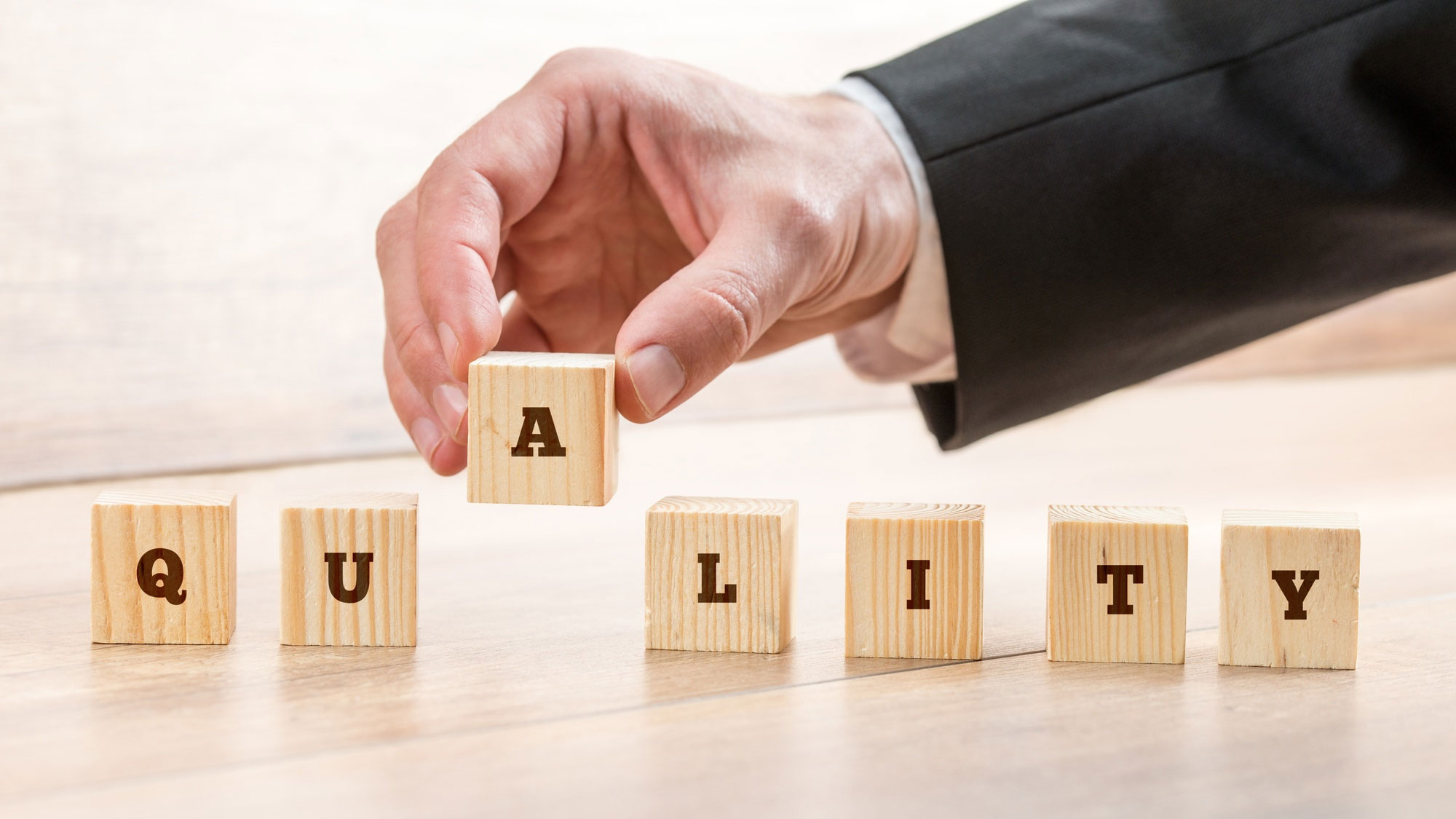
Back to Basics: Quality Assurance vs. Quality Control

Posted by Walid Abou-Halloun Date: Aug 22, 2022 1:00:31 AM
Whether you’re an established company or a small startup, you know firsthand just how important customer satisfaction is to the success of your business.
Before, traditionally, if customers aren’t happy with your products or services, you would probably be the first to know as they would either call your customer service hotline or return the item personally.
But now, if they aren’t satisfied, the world would know about the problem even before you do. How? It’s as easy as logging in to their social media accounts and posting bad reviews on your page. Worse, these negative posts could even go viral and ultimately affect your sales.
What does this tell us? Simple. Businesses need to keep in mind that with the emergence of digital platforms in the market, failure to implement proper quality assurance and quality control strategies can cause serious damage to your brand’s reputation.
So, what can you do to increase customer satisfaction, while also finding ways to streamline your operations, create better products, and lower your production cost?
You don’t need to go that far! Let’s go back to basics and discuss quality assurance (QA) vs. quality control (QC).
QA vs. QC: Key Roles
It’s easy to get quality assurance and quality control mixed up, but they are different in so many ways.
Let’s begin with their key roles.
Quality assurance covers all points within the development of the product, focusing more on the process than on the actual the product itself.
Meanwhile, quality control begins after the manufacturing process and focuses on the actual product itself.
QA vs. QC: Examples
Quality Assurance
Working to ensure that you’re exhausting all possible means to improve the manufacturing process, quality assurance is they key to preventing problems at an early stage.
To identify issues within the product creation, quality assurance seeks to answer questions related to the manufacturing process. Here are some examples:
- Are your manufacturing machines functioning well?
- What can you do to limit the amount of human error in the manufacturing process?
- Has the manufacturer made a change in the materials they use?
- How can you improve a product design to make it easier to use?
- What is causing your e-commerce website to crash frequently?
- How can you eliminate threats to your website regarding customer payment information?
Simply put, if QA teams have a motto, it would be “prevention is better than cure.”
To apply this, QA teams regularly conduct manufacturing tests, spot checks, and other types of audits. These tests will help ensure that the process is working as expected.
Quality Control
On the other hand, quality control serves as the gatekeeper after the process, making sure that the product itself is good-to-go.
Here are some examples where QC is applied:
- Using AI to test a new tech product for bugs
- Conducting software testing
- Inspecting individual products on an assembly line
- Hiring people to proofread product instructions/packaging
- Assigning undercover shoppers in a store to assess customer service
- Taking taste-tests of food served at a restaurant
- Testing airbags, seat belts, or other parts of a car
- Conducting focus groups to learn about product usability
Think of quality control as the examiner of finished products of the processes created and maintained by the QA team.
Quality control is most often a long checklist, a series of tests, or certain activities that are performed to test a product’s overall quality. These specific tests and checklists are defined by the needs of a company, and will vary depending on the product and industry.
In general, QC teams look for product defects, identify where customers’ needs aren’t being fulfilled, and more. Then, based on the findings, they proceed to solving the problems.
As you can see, quality control is more industry-specific than quality assurance.
QA vs. QC: Benefits
Now that we have a better understanding of the main differences of quality assurance and quality control, let’s take a look at the benefits of each to your business.
Quality Assurance
First of all, having a dedicated QA team means that you’ll have employees whose job is solely to focus on the quality of your manufacturing process. This means you’ll be able to catch more errors and therefore, fix more problems early on.
You’ll also be able to streamline your processes by identifying and eliminating potential risks, both in safety and cost. Of course, if risk is managed, you will benefit from lower operating expenses.
Boosting employee productivity is also a benefit of QA, as you can identify what’s slowing down a process and how you can expedite your operations more efficiently.
If properly deployed, QA will help grow your company in no time, while remaining a few steps ahead of the competition.
Quality Control
If there’s one benefit you can get from having a dedicated quality control team, it is preventing costly and reputation-damaging product recalls.
Needless to say, customers will think twice about buying from a brand that puts consumers at risk.
Anything you can do to avoid a product recall, or at least lessen its number, is absolutely essential to the success of your business.
Additionally, quality control will promote customer satisfaction. No parent would want to buy their kid a toy that breaks within the first week of purchase. No professional would choose to purchase an electronic gadget from a brand that has poor after-sales service and doesn’t seem to listen to customer feedback.
Conducting regular QC is a way to get to know your market better. What features do they like the most about your product? Which areas need further improvement?
This won’t only increase your brand’s authority in your industry and boost your customer loyalty, it will also make your advertising strategies a lot more effective.
Ultimately, it goes without saying that developing consumer trust through strong QC methods can help skyrocket your profits.
With these very defined roles, both QA and QC are non-negotiables FOR business success.
QA vs. QC: Conclusion
Just remember: quality assurance focuses on the process, while quality control focuses on the actual product.
While it might be tempting to try to get away with having only one of these processes, deploying dedicated QA and QC teams for your business is an investment that surely pays off in no time.
Where Can You Find QC and QA Services?
If you’re looking for reliable quality assurance and quality control services, we can help you find your perfect fit.
Get in touch with us today.